Шпоночная сталь: свойства, применение, преимущества
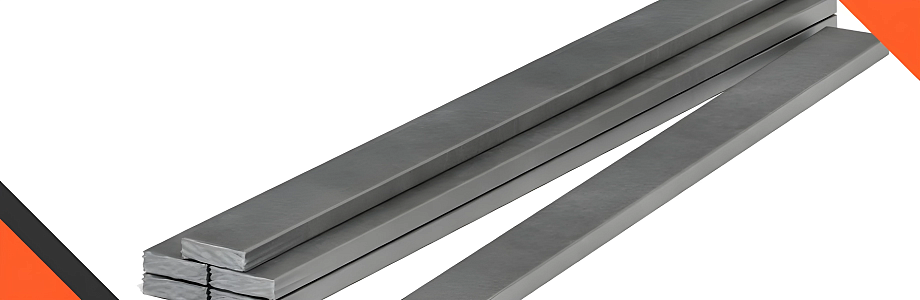
Шпоночная сталь — это высококачественный материал, применяемый для изготовления шпонок, которые являются важными элементами в различных механических и промышленных конструкциях. Эти соединительные детали обеспечивают надежное крепление между валами и другими механическими компонентами, что особенно критично при передаче крутящего момента, сопротивлении различным нагрузкам и предотвращении смещений деталей. В условиях интенсивной эксплуатации оборудования, надежность шпоночного соединения играет ключевую роль в обеспечении долговечности и стабильности работы.
В промышленности и машиностроении особенно важно использовать материалы шпонок, обладающие высокими эксплуатационными характеристиками. Шпоночная сталь ГОСТ 8787-68, как один из таких материалов, позволяет создавать прочные и надежные соединения, что делает её незаменимой в ряде производственных процессов.
Характеристики и свойства
Шпоночная сталь обладает рядом уникальных свойств, которые делают её предпочтительным материалом для изготовления шпонок. Одним из главных свойств является высокая прочность, что позволяет шпонкам выдерживать значительные механические нагрузки без деформации и разрушения. Этот параметр особенно важен в условиях, где соединение подвергается постоянным или переменным нагрузкам.
Шпоночные соединения часто работают в условиях высокой интенсивности, где важна способность материала сохранять свои свойства на протяжении долгого времени. Износостойкая шпоночная сталь значительно увеличивает срок службы соединений, снижая необходимость частого обслуживания и замены деталей.
В условиях эксплуатации, где соединения подвергаются резким и мощным воздействиям, важно, чтобы она не разрушалась и сохраняла свои механические свойства. Это особенно актуально для машиностроения и тяжелой промышленности, где ударные нагрузки могут возникать регулярно.
Обрабатываемость позволяет легко изготавливать изделия из нержавеющей стали различных форм и размеров, что важно для адаптации под конкретные задачи. Это свойство облегчает процесс производства и установки шпонок, снижая затраты времени и усилий.
Типы и марки
Шпоночная сталь делится на несколько типов в зависимости от состава и области применения. Среди основных типов можно выделить углеродистые, легированные и нержавеющие стали, каждая из которых имеет свои преимущества и используется в определенных условиях эксплуатации.
- Углеродистые стали являются наиболее распространенным типом шпоночного материала. Эти стали обладают достаточной прочностью и устойчивостью к механическим воздействиям, что делает их подходящими для большинства стандартных условий эксплуатации. Углеродистая шпоночная сталь широко применяется в машиностроении и промышленности.
- Легированные стали отличаются повышенными характеристиками прочности и устойчивости к агрессивным средам. Эти стали содержат легирующие элементы, такие как хром, никель, молибден и другие, которые значительно улучшают свойства материала. Легированные используются в условиях, где необходима повышенная стойкость к коррозии, износу и механическим нагрузкам.
- Нержавеющие стали — это особый тип шпоночного материала, который используется в условиях повышенной влажности, агрессивных сред и где необходима высокая коррозионная стойкость. Применяется в пищевой, химической и фармацевтической промышленности, а также в машиностроении, где необходима долгосрочная защита от коррозии.
Каждый тип шпоночной стали имеет свои особенности и преимущества, что позволяет выбирать материал в зависимости от конкретных условий эксплуатации. Такой подход гарантирует максимальную эффективность и долговечность шпоночных соединений.
Для чего нужны шпонки и их функции
Шпонки выполняют важную функцию в механических соединениях, обеспечивая передачу крутящего момента между валом и насаженной деталью. Этот процесс необходим для передачи движения и силы от одного элемента к другому, что особенно важно в машиностроении, где используются различные вращающиеся механизмы. Шпоночное соединение применяют для фиксации деталей на валу, что предотвращает их проскальзывание и смещение во время работы.
На рынке представлены различные виды шпонок, которые применяются в зависимости от конструктивных особенностей и условий эксплуатации. Среди них можно выделить следующие разновидности шпонок:
- Клиновая шпонка — используется для создания особенно прочных соединений, где требуется надежная фиксация деталей. Она имеет форму клина и обеспечивает плотное прилегание к поверхности вала и насаженной детали.
- Цилиндрическая шпонка — применяется для соединения деталей с гладкими цилиндрическими поверхностями. Это простой и эффективный тип шпонки, который часто используется в стандартных механических соединениях.
- Металлическая шпонка — изготавливается из различных видов стали, что позволяет использовать её в широком спектре приложений. Этот тип отличается высокой прочностью и долговечностью.
Каждый вид имеет свои особенности и области применения, что позволяет выбирать оптимальное решение в зависимости от конкретных задач.
Достоинства и недостатки
Шпоночные соединения имеют ряд преимуществ, благодаря которым они остаются востребованными в машиностроении и промышленности:
- Простота конструкции и изготовления. Отличаются минимализмом в своей конструкции. Основные элементы — вал, шпонка и насаженная деталь — легко поддаются обработке и не требуют сложного оборудования для производства. При этом пазы для шпонок можно фрезеровать на стандартных станках, что снижает себестоимость и ускоряет процесс производства. Благодаря простоте конструкции, такие соединения массово применяются в различных отраслях — от автомобильной промышленности до станкостроения.
- Высокая надежность и долговечность. Применение шпоночной стали ГОСТ 8787-68 обеспечивает стабильные эксплуатационные характеристики даже в условиях значительных механических нагрузок и вибраций. Стальные шпонки, благодаря своим свойствам, могут выдерживать многократные циклы нагружения без значительного износа, что важно для механизмов, работающих в условиях переменных и ударных нагрузок.
- Передача значительных крутящих моментов. Эффективно передают большие крутящие моменты за счет высокой контактной поверхности между шпонкой, валом и насаженной деталью. Для сравнения, шлицевые соединения требуют большего числа зубьев и более сложного процесса изготовления, в то время как одна шпонка может выполнять аналогичную функцию. Например, в типичных редукторах с мощностью до 200 кВт шпонки часто применяются для передачи усилий от вала к шестерням или другим элементам привода.
Тем не менее существуют и некоторые ограничения:
- Ослабление конструкции вала. Для установки на вале необходимо вырезать паз, что приводит к локальному снижению прочности вала. Степень ослабления зависит от диаметра вала и глубины паза. Например, при глубине паза, составляющей 1/4 диаметра вала, ослабление может достигать 10-20%. Это требует дополнительных расчетов при проектировании валов, особенно в высоконагруженных узлах.
- Концентрация напряжений. В области паза шпонки возникают локальные концентрации напряжений, что повышает риск возникновения трещин и других дефектов. Для минимизации этих рисков необходимо учитывать геометрию и качество обработки паза. В условиях динамических нагрузок (например, при частых пусках и остановках механизма) концентрация напряжений может значительно снизить срок службы соединения.
- Сложность монтажа и демонтажа. Установка и снятие шпонки требует определенных навыков и инструментов. Особенно это касается клиновых шпонок, которые могут быть трудно извлекаемы из-за плотной посадки. В некоторых случаях демонтаж сопровождается повреждением шпонки или деталей, что требует замены компонентов. В отличие от шлицевых соединений, где демонтаж можно произвести быстрее, шпоночные соединения требуют более аккуратного подхода.
Для тех, кто заинтересован в приобретении надежных материалов и крепежных изделий для создания шпоночных соединений, интернет-магазин Krepco предлагает обширный каталог товаров, включающий шпоночную сталь, крепеж и изделия из нержавеющей стали. Здесь можно купить продукцию, отвечающую высоким стандартам качества и надежности.
Удобный заказ и быстрая доставка по всей России обеспечат оперативное получение нужных материалов. В каталоге интернет-магазина представлено множество позиций с доступными ценами, что позволяет выбрать оптимальное решение для различных задач.
Шайбы
Шайбы выполняют несколько важных функций:
- Распределение нагрузки. Увеличивают площадь контакта между саморезом и поликарбонатом, равномерно распределяя нагрузку и предотвращая деформацию материала.
- Защита от повреждений. Предотвращают продавливание поликарбоната головкой самореза, что может привести к появлению трещин и нарушению герметичности.
Виды:
- Плоские применяются для крепления поликарбоната к металлическому каркасу.
- Конические используются для крепления к деревянному каркасу, обеспечивая плотное прилегание к поверхности.
Термошайбы необходимы для компенсации термического расширения поликарбоната, особенно при использовании в конструкциях, подверженных значительным перепадам температур.
Шурупы, болты и гвозди
Шурупы, болты и гвозди для поликарбоната могут использоваться для крепления, однако они не являются оптимальным решением. Эти виды крепежа не обеспечивают достаточной герметичности и могут повредить материал при неправильной установке. Шурупы для поликарбоната не компенсируют термическое расширение, что может привести к деформации и разрушению конструкции.
Другие типы крепежа
Помимо саморезов и шайб, для крепления используются и другие специализированные элементы:
- Соединительные профили применяются для соединения листов поликарбоната между собой, обеспечивая герметичность и эстетичный вид конструкции.
- Торцевые профили защищают края поликарбоната от попадания влаги, пыли и насекомых, предотвращая его разрушение.
- Уплотнительные ленты используются для герметизации стыков и швов, предотвращая протекание воды и проникновение холодного воздуха.
- Клей применяется для склеивания листов между собой или с другими материалами, обеспечивая прочное и герметичное соединение.
Выбор самореза и шурупа зависит от множества факторов, таких как тип конструкции, материал каркаса, толщина поликарбоната, условия эксплуатации и другие.
Чем и как крепить поликарбонат
Выбор крепежных элементов и метода крепления поликарбоната зависит от типа каркаса, к которому будет фиксироваться поликарбонат, и от условий эксплуатации сооружения.
К деревянной конструкции
Для крепления поликарбоната к деревянным элементам используют саморезы по дереву с прессшайбой. Этот тип саморезов специально разработан для работы с древесиной и отличается наличием самонарезающей резьбы, которая позволяет легко вкручивать их в материал без предварительного сверления. Прессшайба обеспечивает герметичность соединения и предотвращает повреждение поликарбоната при затягивании самореза.
Диаметр подбирается в зависимости от толщины поликарбоната и обычно составляет 4,8-6,3 мм. Длина саморезов должна быть достаточной для прохождения через поликарбонат и надежного закрепления в деревянном каркасе.
Как правильно установить поликарбонат? Перед монтажом необходимо предварительно просверлить отверстия в листах. Диаметр отверстий должен быть на 2-3 мм больше диаметра самореза, чтобы учесть термическое расширение материала. Это предотвратит деформацию и повреждение поликарбоната при изменении температуры.
К металлу
При креплении поликарбоната к металлу применяются саморезы по металлу с прессшайбой. Они отличаются от саморезов по дереву наличием более острой резьбы, которая позволяет легко проникать в металл. Для обеспечения надежного крепления и предотвращения коррозии также рекомендуется использовать крепежи из нержавеющей стали.
Для создания герметичного соединения и защиты от попадания влаги и пыли под крепеж, рекомендуется использовать специальные прокладки. Это могут быть резиновые или неопреновые прокладки, которые устанавливаются между шайбой и поликарбонатом. Прокладки обеспечивают дополнительную защиту от протечек и увеличивают срок службы конструкции.
К бетонной поверхности
Крепление поликарбоната к бетонной поверхности требует использования специальных крепежных элементов, таких как дюбель-гвозди или болты для крепления поликарбоната. Дюбель-гвозди представляют собой комбинацию пластикового дюбеля и металлического гвоздя. При забивании гвоздя дюбель расширяется, обеспечивая надежную фиксацию в бетоне. Анкерные болты имеют более сложную конструкцию и обеспечивают более прочное крепление, особенно при больших нагрузках.
Перед установкой крепежа в бетонную поверхность необходимо просверлить отверстия, диаметр которых должен соответствовать диаметру дюбеля или анкера. Затем в отверстие вставляется дюбель или анкер, и поликарбонат крепится с помощью саморезов с прессшайбой. Для обеспечения герметичности соединения рекомендуется использовать резиновые или неопреновые прокладки.
Для получения подробной информации о видах, материалах и применении болтов, рекомендуем прочитать статью: какие бывают болты: виды, материалы, прочность, покрытия и применение.
Что необходимо учитывать при выборе крепежа
При выборе необходимо учитывать ряд важных факторов, которые влияют на эффективность и долговечность крепления.
Размер и толщина
Толщина является одним из ключевых факторов при выборе крепежа. Для тонких листов (4-6 мм) подойдут саморезы длиной 25-35 мм с диаметром 4,8 мм, а для более толстых (8-10 мм) – 45-55 мм с диаметром 5,5 или 6,3 мм. Использование саморезов неподходящей длины может привести к недостаточной прочности крепления или повреждению поликарбоната.
Особенности конструкции
Тип каркаса (деревянный, металлический или бетонный), его форма, размеры и предполагаемые нагрузки на конструкцию также играют важную роль при выборе крепежа. Для небольших конструкций, таких как теплицы или навесы, достаточно использовать саморезы с прессшайбой. Однако, для более крупных и нагруженных конструкций, например, навесов для автомобилей или бассейнов, может потребоваться использование более прочного крепежа, такого как анкерные болты с диаметром 8-10 мм и длиной, соответствующей толщине несущей конструкции.
Для крепления поликарбоната к профилированным листам или трубам могут потребоваться специальные саморезы с уменьшенной головкой (например, саморезы DIN 7982С) или саморезы со сверломм (например, саморезы DIN 7504K), позволяющие просверлить отверстие в металле без предварительной подготовки.
Качество крепежа
Рекомендуется выбирать крепеж из нержавеющей стали марки A2 или A4, например, оцинкованные (класс покрытия 8.8) или с покрытием из желтого цинка (класс покрытия 5.8). Это обеспечит защиту от коррозии и увеличит срок службы крепежных элементов до 50 лет и более.
Она должна быть изготовлена из прочного и эластичного материала, такого как ТРЕ или EPDM, а также температурным перепадам от -40°C до +120°C. Качественная прессшайба обеспечит герметичность соединения и предотвратит повреждение поликарбоната.
Статья о том, что такое строительная шайба: особенности и виды, основные функции и применение поможет разобраться в разнообразии шайб и выбрать подходящий вариант. Правильно подобранный и установленный крепеж – залог долговечности и безопасности конструкции из поликарбоната.
Где купить
В каталоге интернет магазина https://www.krepco.ru/ представлены крепежные элементы различных типов: саморезы, болты, шайбы и другие изделия, специально предназначенные для работы с поликарбонатом. Квалифицированные специалисты магазина Крепко всегда готовы помочь вам с выбором, предоставив профессиональную консультацию и необходимую информацию о товаре.
Для удобства клиентов в интернет-магазине предусмотрена возможность заказа крепежа с доставкой по всей России. Это значит, что вы можете получить необходимые крепежные изделия прямо на объект строительства или домой, не тратя время на поиски в обычных магазинах.
Цены формируются с учетом потребностей широкого круга потребителей, благодаря чему можно подобрать оптимальные решения как для мелких, так и для крупных строительных проектов.
Затрудняетесь с выбором?
Позвоните нам, вы получите квалифицированную консультацию и мы поможем сделать лучший выбор.
Заказать обратный звонок